814jeffw
Active member
I am going to buy a Titan hose reel,..I am getting the upgraded SS manifold. This is going to be used for roof cleaning, so, even though it's SS,..it will most likely need replaced at some point. Anyone with experience in replacing the manifold? Just want to know the difficulty level,.. Just by looking I can't imagine it's that difficult. The reel I have now is a reel I made and was made to replace the manifold easily. Any input would be appreciated.
*On the same topic, the elbow that connects your hose to the reel can be turned to run the same direction as the spool. This creates a way better transition than the more common position of the elbow,..that goes against the grain as I like to call it. I also use a conduit clamp on the hose near the main connection, which takes any strain from the connection. I also cut a small piece of PVC pipe and then pit it so it makes a cover for the connection so the the hose isn't getting pinched down onto the connection as it's wrapped. The PVC pipe makes it nice and rounded.
**The weld isn't part of the fluid connection, it is there to stabilize the connection and is simply cut off when replacing the manifold.
Jeff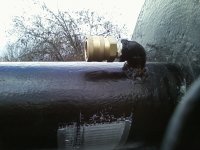
*On the same topic, the elbow that connects your hose to the reel can be turned to run the same direction as the spool. This creates a way better transition than the more common position of the elbow,..that goes against the grain as I like to call it. I also use a conduit clamp on the hose near the main connection, which takes any strain from the connection. I also cut a small piece of PVC pipe and then pit it so it makes a cover for the connection so the the hose isn't getting pinched down onto the connection as it's wrapped. The PVC pipe makes it nice and rounded.
**The weld isn't part of the fluid connection, it is there to stabilize the connection and is simply cut off when replacing the manifold.
Jeff
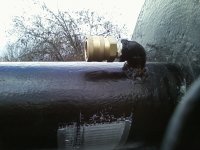
Last edited: